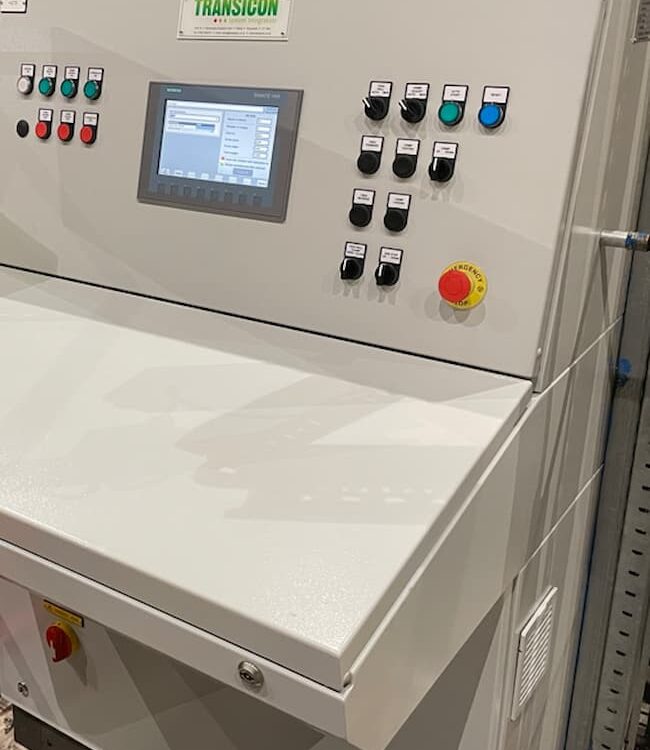
The Challenge
- A leading manufacturer of steel building system profile Asked Transicon to upgrade a machine used to bend profiled sheets to form connecting corners. The machine used drives coupled to a basic text Man Machine Interface (MMI).
- The customer was losing significant time due to the machine malfunctioning, plus a difficult and time-consuming recovery process if the machine was ever stopped mid-operation.
- The drives were obsolete, and the AC motors used for positioning did not meet our customer’s accuracy requirements.
- Each time tooling was changed, the machine needed to be set up for the next product using adjustment by trial-and-error, which was time consuming and wasted a lot of material as scrap
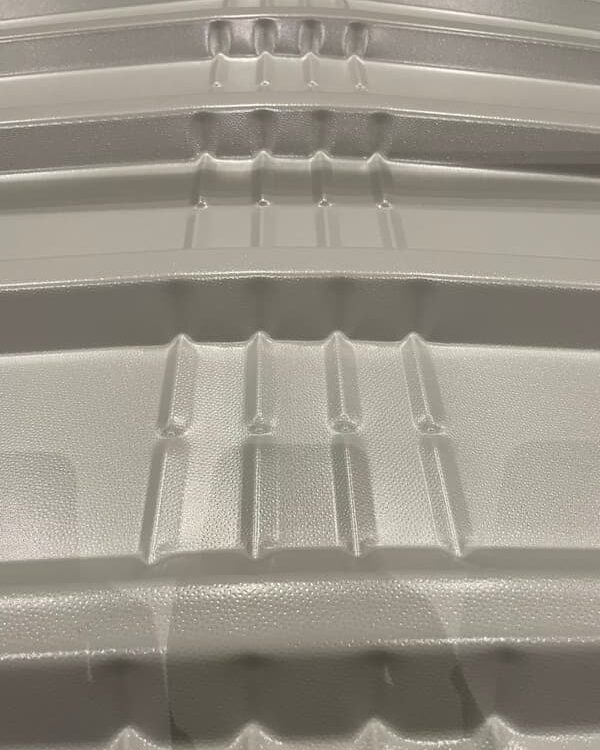
Transicon's Solution
- Transicon provided a new control system, which used all existing wiring and sensors for quick installation and commissioning.
- AC motors were replaced with Bosch Rexroth Servo motors and drives coupled to backlash-free Wittenstein gearboxes, resulting in high levels of precision and repeatability. The improved control of the servo system also allowed the machine to run at increased speed, improving output.
- Usability of the system was greatly increased thanks to a new Siemens Safe PLC and HMI. A recipe system was introduced, meaning the machine was automatically reconfigured for the new tooling and ready to operate without the need for trial-and-error setup, vastly reducing wasted material.
- The new PLC software also allowed the machine to be restarted with the push of a button from any interruption mid-operation, again reducing wasted staff-hours.